What Is the Hum in a Transformer
Transformers are essential components in electrical power systems, but their characteristic humming noise can sometimes cause concern or indicate potential issues. This article explores the various causes behind transformer hum, from magnetostriction and loose laminations to vibrations from auxiliary components and electrical factors.
We will also discuss practical remedies and mitigation techniques to address these issues, ensuring optimal transformer performance and longevity.
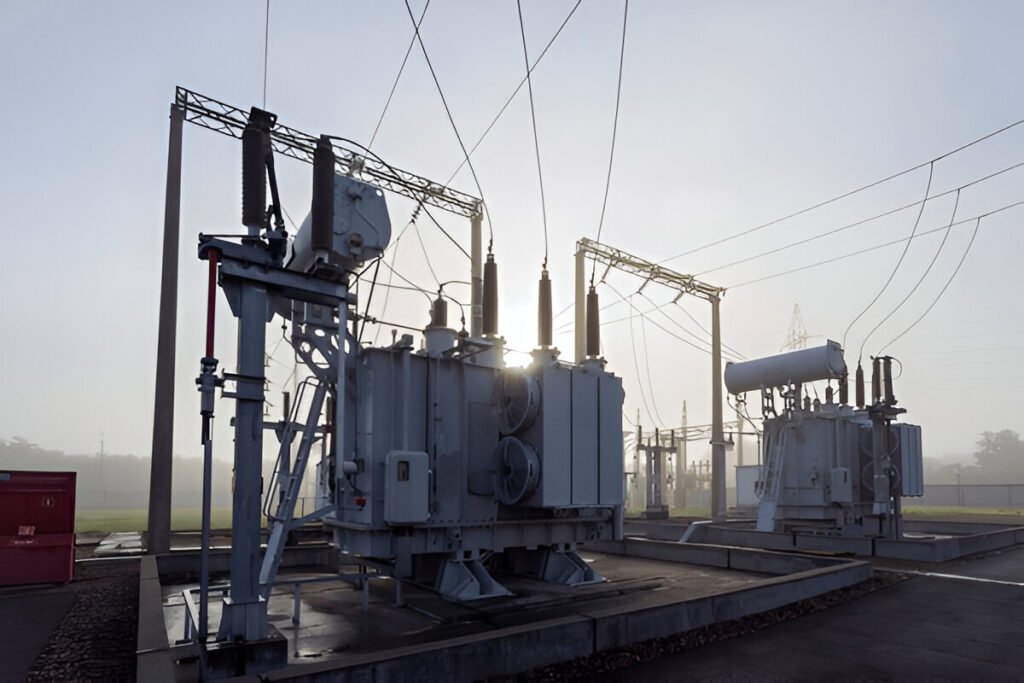
Magnetostriction
Magnetostriction is a phenomenon that occurs in ferromagnetic materials, such as the core laminations of a transformer, when they are subjected to a magnetic field. The magnetic field causes the material to expand and contract slightly, leading to mechanical vibrations that produce an audible humming noise. The intensity of the magnetostriction-induced hum depends on factors such as the material properties, the magnetic field strength, and the frequency of the applied voltage.
In transformers, magnetostriction is more pronounced in the core laminations near the top and bottom yokes, where the magnetic flux density is highest. The vibrations caused by magnetostriction can be transmitted to the transformer tank and other structural components, amplifying the humming noise. Magnetostriction is an inherent property of the core material and cannot be completely eliminated, but it can be minimized through proper design and material selection.
Loose Laminations
Loose laminations in the transformer core can also contribute to the humming noise. Laminations are thin sheets of electrical steel that are stacked and insulated from each other to form the transformer core. If the laminations are not properly tightened or if the insulation between them deteriorates over time, they can vibrate against each other, creating a humming sound.
Loose laminations can be caused by several factors, including:
- Improper core assembly during manufacturing
- Damage during transportation or installation
- Aging and deterioration of the insulation material
- Excessive mechanical stress due to short-circuit forces or thermal cycling
To minimize the effects of loose laminations, manufacturers use various techniques, such as step-lap joints, bonding, and clamping, to ensure a tight and stable core assembly. Regular maintenance and inspection can also help identify and address loose laminations before they cause significant issues.
Vibrations from Auxiliary Components
Transformers often have auxiliary components, such as cooling fans, pumps, and control cabinets, mounted on or near the transformer tank. These components can generate their own vibrations, which can couple with the transformer and contribute to the overall humming noise.
Cooling fans, for example, are used to circulate air and dissipate heat from the transformer. The rotating blades of the fans can create turbulence and pressure fluctuations, which can excite the transformer tank and cause it to vibrate. Similarly, pumps used in oil-filled transformers for oil circulation can also generate vibrations due to their mechanical motion.
To mitigate the effects of auxiliary component vibrations, manufacturers use vibration isolation techniques, such as:
- Rubber or spring mounts for fans and pumps
- Flexible couplings for connecting components to the transformer
- Acoustic enclosures or barriers to contain the noise
- Optimizing the placement and orientation of components to minimize vibration transmission
Electrical Causes
In addition to mechanical causes, transformer hum can also be influenced by electrical factors. One such factor is the presence of harmonic currents in the transformer windings. Harmonic currents are multiples of the fundamental frequency (50 or 60 Hz) and are caused by non-linear loads, such as power electronic devices, connected to the power system.
Harmonic currents can cause additional losses in the transformer windings and core, leading to increased heating and vibrations. They can also create unbalanced magnetic forces in the transformer, which can exacerbate the humming noise. To reduce the impact of harmonic currents, power system engineers use various techniques, such as:
- Installing harmonic filters to suppress the harmonic components
- Using phase-shifting transformers to cancel out specific harmonics
- Employing active power filters to compensate for the harmonic currents
- Designing the transformer with higher impedance to limit the flow of harmonic currents
DC Offset
Another electrical cause of transformer hum is the presence of DC offset in the transformer windings. DC offset can occur due to various reasons, such as geomagnetically induced currents (GICs) during solar storms, asymmetrical firing of power electronic devices, or the use of half-wave rectifiers. DC offset can cause the transformer core to saturate asymmetrically, leading to increased magnetostriction and vibrations.
To mitigate the effects of DC offset, transformers can be designed with:
- Air gaps in the core to prevent saturation
- DC blocking devices, such as capacitors or chokes, to prevent the flow of DC currents
- Neutral grounding resistors to provide a path for DC currents and limit their magnitude
- Monitoring systems to detect and alert operators about the presence of DC offset
Remedies and Mitigation Techniques
Improved Core Materials and Design
Advancements in core materials and design have played a significant role in reducing transformer hum. Manufacturers now use high-grade, grain-oriented electrical steel (GOES) with better magnetic properties and lower losses. GOES is produced with tighter control over the grain structure and orientation, resulting in reduced magnetostriction and core losses.
Transformer cores are also designed with step-lap joints or mitred joints to minimize air gaps and ensure a more uniform magnetic flux distribution. These joint designs help reduce local flux concentrations and the associated vibrations. Additionally, cores are often constructed with a higher stacking factor, meaning the laminations are more tightly packed, which reduces the potential for loose laminations and vibrations.
Vibration Damping and Isolation
Vibration damping and isolation techniques are employed to minimize the transmission of vibrations from the transformer to the surrounding environment. One common approach is to use vibration isolation pads or mounts between the transformer and its foundation. These pads, made of rubber or other elastomeric materials, absorb and dissipate the vibrational energy, reducing the overall noise level.
Transformer tanks can also be designed with additional stiffening ribs or reinforcements to increase their rigidity and reduce vibrations. The use of constrained layer damping (CLD) materials, such as viscoelastic sheets or coatings, can further absorb and dissipate vibrational energy.
Active Noise Control
Active noise control (ANC) is an advanced technique that uses sound waves to cancel out the transformer hum. ANC systems employ microphones to measure the humming noise and generate an “anti-noise” signal that is 180 degrees out of phase with the original noise. When the anti-noise signal is emitted through speakers, it interferes with the transformer hum, effectively canceling it out.
ANC systems can be particularly effective in reducing low-frequency hum, which is often the most difficult to mitigate using passive methods. However, ANC systems require careful design and calibration to ensure optimal performance and avoid unintended consequences, such as creating additional noise in other frequency ranges.
Regular Maintenance and Monitoring
Regular maintenance and monitoring of transformers can help identify and address issues related to transformer hum before they become more severe. This includes:
- Periodic inspections of the transformer core and windings to check for loose laminations, insulation damage, or other mechanical issues
- Monitoring of the transformer’s vibration levels using accelerometers or other sensors to detect abnormal vibrations or trends
- Analysis of the transformer’s sound frequency spectrum to identify specific components or frequencies contributing to the hum
- Regular testing and maintenance of auxiliary components, such as cooling fans and pumps, to ensure they are operating properly and not contributing to excessive vibrations
By implementing a comprehensive maintenance and monitoring program, power system operators can proactively address transformer hum issues and maintain the overall reliability and efficiency of the power system.