
Guide to Transformer Efficiency
Have you ever wondered how transformers manage to supply power efficiently to our homes and industries? To grasp the essence of transformer efficiency, you’ll need to understand the interplay of factors like core material, winding design, and load conditions.
In the following sections, we’ll explore the key concepts and formulas that underpin transformer efficiency, empowering you to make informed decisions when selecting or evaluating these critical components of our electrical infrastructure.
Fundamentals of Transformer Efficiency
What is Transformer Efficiency
Transformer efficiency is a measure of how effectively a transformer converts electrical energy from its primary winding to its secondary winding. It is the ratio of the output power delivered by the transformer to the input power supplied to it, expressed as a percentage. A higher efficiency indicates that less energy is lost during the transformation process, resulting in better performance and cost savings.
Formula For Calculating Efficiency
Efficiency (η) = (Output Power / Input Power) × 100%
Where:
- Output Power is the power delivered by the secondary winding of the transformer to the load.
- Input Power is the power supplied to the primary winding of the transformer.
To calculate the efficiency, measure the voltage and current at both the primary and secondary windings of the transformer under load conditions. The power can then be calculated using the formula:
Power = Voltage × Current
For example, if the primary winding of a transformer is supplied with 220V and draws a current of 5A, while the secondary winding delivers 200V at 4.5A to the load, the efficiency can be calculated as follows:
Input Power = 220V × 5A = 1100W
Output Power = 200V × 4.5A = 900W
Efficiency (η) = (900W / 1100W) × 100% = 81.82%
In this case, the transformer has an efficiency of 81.82%, meaning that 81.82% of the input power is successfully transferred to the output, while the remaining 18.18% is lost as heat and other losses within the transformer.
Condition for Maximum Efficiency
A transformer achieves maximum efficiency when the variable copper losses equal the constant iron losses. At this point, the total losses are minimized, resulting in the highest possible efficiency for the transformer.
To achieve maximum efficiency, the transformer must be designed and operated under specific conditions:
- Proper sizing: The transformer should be sized appropriately for the intended load to minimize losses.
- Optimal flux density: The flux density in the core should be kept within the optimal range to minimize core losses.
- Load matching: The transformer should be operated at or near its rated load to balance copper and iron losses.
- Quality materials: Using high-quality, low-loss materials for the core and windings can help reduce losses and improve efficiency.

Types of Losses in Transformers
Copper losses (load losses)
Copper losses in transformers, also known as load losses, occur when current flows through the primary and secondary windings. The resistance in these windings causes power dissipation, leading to inefficiency in the transformer’s operation. The magnitude of copper losses is proportional to the square of the load current, making them a significant concern at higher loads.
Core losses (no-load losses)
Core losses, also known as no-load losses, occur in transformers even when they are not supplying any load. These losses take place in the laminated steel core and are caused by two phenomena: hysteresis and eddy currents.
Eddy current losses occur when alternating magnetic fields induce circulating currents in the transformer core. These currents, known as eddy currents, flow in closed loops perpendicular to the magnetic field, causing resistive heating and reduced efficiency. The power dissipated by eddy currents is proportional to the square of the frequency and the thickness of the core laminations.
Hysteresis losses result from the magnetization and demagnetization of the transformer core during each alternating current (AC) cycle. As the magnetic field alternates, the magnetic domains in the core material realign, consuming energy. The power dissipated due to hysteresis is proportional to the frequency and the area of the hysteresis loop, which depends on the core material properties.
Stray losses
Stray losses in transformers occur due to various factors beyond eddy current and hysteresis losses. These losses can be detected by thermal relays, which are sensitive to partial discharge and voltage impulses. Stray losses cause transformer oil to degrade over time, reducing the transformer’s efficiency.
Dielectric losses
Dielectric losses in transformers occur when the alternating electric field heats the insulation materials. This type of loss affects both dry-type and liquid-filled transformers.
In dry-type transformers, air serves as the primary insulation medium. The air gaps between windings and core components can lead to higher dielectric losses compared to liquid-filled transformers.
Liquid-filled transformers, such as those using mineral oil or synthetic esters, benefit from the insulating liquid’s higher dielectric strength and better heat dissipation. This helps to reduce dielectric losses and improve overall transformer performance.
To reduce dielectric losses, manufacturers apply protective coatings around terminals and transformer bushings.
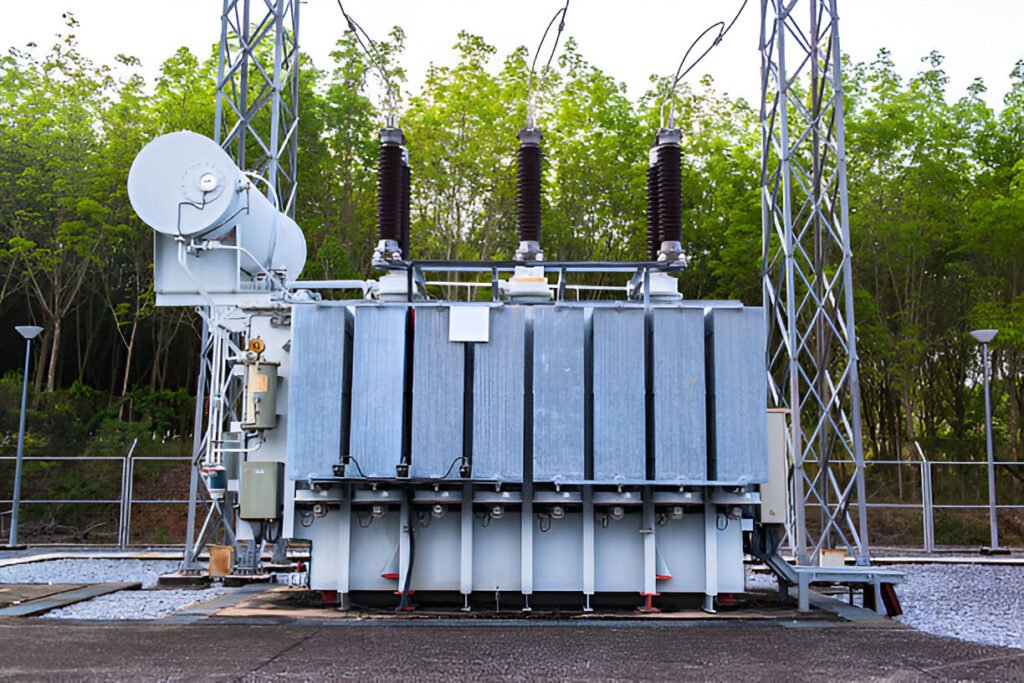
Efficiency Standards and Regulations
- IEC 60076-20:2017: This international standard, developed by the International Electrotechnical Commission (IEC), specifies the energy efficiency requirements for power transformers with a minimum power rating of 25 kVA and a highest voltage for equipment not exceeding 36 kV.
- IEEE C57.120-2017: The Institute of Electrical and Electronics Engineers (IEEE) standard establishes the minimum efficiency levels for low-voltage dry-type distribution transformers with ratings from 15 to 333 kVA and a primary voltage of 600 V or less.
- DOE 10 CFR Part 431: The U.S. Department of Energy (DOE) has set mandatory energy conservation standards for distribution transformers manufactured or imported into the United States. These standards apply to liquid-immersed and medium-voltage dry-type distribution transformers with ratings ranging from 10 to 2,500 kVA.
- NEMA TP 1-2002: The National Electrical Manufacturers Association (NEMA) has established a voluntary standard for the efficiency of low-voltage dry-type distribution transformers. This standard has been widely adopted in the United States and has served as the basis for the DOE’s mandatory standards.
- EU Ecodesign Directive (2009/125/EC): The European Union’s Ecodesign Directive sets mandatory ecological requirements for energy-related products, including power transformers. The directive aims to reduce the environmental impact of these products by improving their energy efficiency and reducing greenhouse gas emissions.
Factors Influencing Transformer Efficiency
- Transformer design and construction: The overall design and construction quality of a transformer play a crucial role in its efficiency. Factors such as the core material, winding configuration, and insulation quality all contribute to the transformer’s performance and efficiency.
- Core material and geometry: High-quality, grain-oriented silicon steel cores with optimized lamination thickness and stacking techniques minimize core losses and improve efficiency. The core cross-sectional area and the number of turns in the windings also affect efficiency.
- Winding configuration and conductor sizing: The winding configuration, such as the type of winding (disc or layer), the number of turns, and the cross-sectional area of the conductors, impacts transformer efficiency. Proper conductor sizing and the use of high-quality materials minimize copper losses and enhance efficiency.
- Insulation quality and cooling system: Proper insulation prevents dielectric losses and ensures reliable operation. Efficient cooling systems, such as oil or air cooling, help dissipate heat generated by the transformer, reducing the risk of overheating and maintaining optimal efficiency.
- Load characteristics and operating conditions: The load characteristics and operating conditions significantly affect transformer efficiency. The load level, power factor, and the presence of harmonics or non-linear loads can impact efficiency. Transformers achieve maximum efficiency when operating near their rated capacity and with a high power factor.
- Ambient temperature and altitude: High ambient temperatures increase winding resistance and reduce cooling effectiveness, leading to increased losses. Similarly, transformers operating at high altitudes may experience reduced cooling efficiency due to the lower air density.

Measuring and Evaluating Transformer Efficiency
Standard Test Methods (Open-Circuit and Short-Circuit Tests)
The open-circuit test, also known as the no-load test, is performed by applying the rated voltage to the primary winding while leaving the secondary winding open. This test helps determine the core losses of the transformer.
The short-circuit test is conducted by short-circuiting the secondary winding and applying a reduced voltage to the primary winding. This test allows for the measurement of copper losses in the transformer.
Efficiency Calculation from Test Data
The data obtained from the open-circuit and short-circuit tests can be used to calculate the efficiency of the transformer. The core losses, measured during the open-circuit test, and the copper losses, determined through the short-circuit test, are combined with the output power to calculate the efficiency using the following formula:
Efficiency = Output Power / (Output Power + Core Losses + Copper Losses)
Efficiency Metrics for Distribution Transformers
One commonly used metric is peak efficiency, which represents the highest efficiency achieved by the transformer at a specific loading condition.
Another important metric is the weighted average efficiency, which takes into account the transformer’s efficiency across a range of loading conditions. This metric provides a more comprehensive assessment of the transformer’s overall performance in real-world applications.
Weighted average efficiency is calculated by assigning weights to different loading levels based on their expected frequency of occurrence and then averaging the efficiencies at those loading levels.
FAQs
Are transformers 100% efficient?
No, transformers are not 100% efficient. They experience energy losses due to factors such as winding resistance, core losses, and leakage reactance. However, well-designed transformers can achieve efficiencies up to 99% under optimal conditions.
Why is the efficiency of a transformer as high as 97%?
Transformers achieve high efficiencies due to their design and construction. They use high-quality materials, such as low-resistance windings and low-loss core materials, to minimize energy losses. Additionally, transformers have no moving parts, which reduces friction and mechanical losses.
Which transformer has 100% efficiency?
No transformer has 100% efficiency. Even under ideal conditions, there will always be some energy losses due to the physical properties of the materials used in the transformer’s construction. The highest achievable efficiency for a well-designed transformer is around 99%.