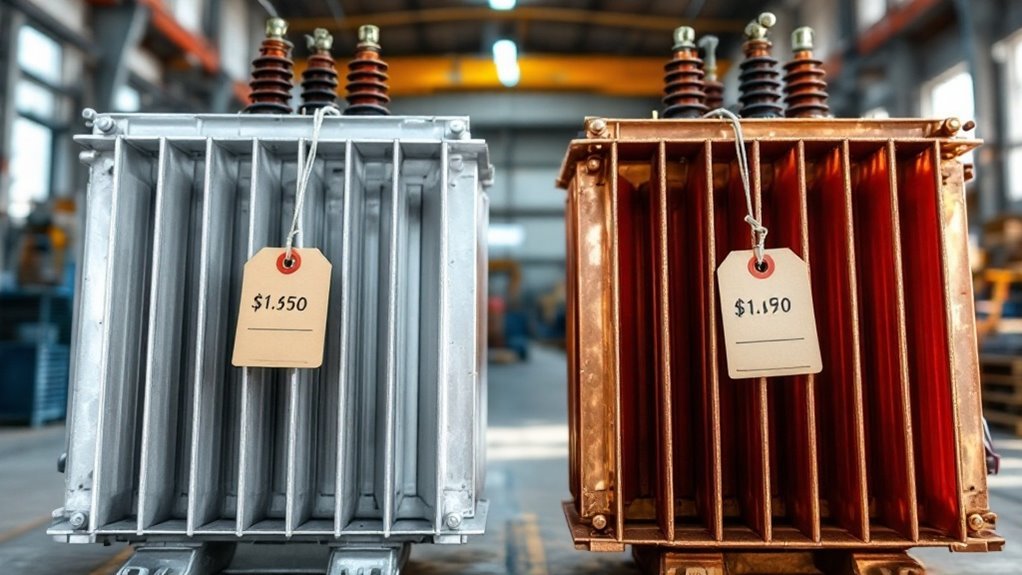
What Is the Difference Between Aluminium Transformer and Copper Transformer
Power transformers represent one of the most significant components in electrical distribution systems, with material selection directly impacting performance and cost-effectiveness. The ongoing debate between aluminum and copper transformers has shaped purchasing decisions across industries, from utility companies to manufacturing facilities.
This comprehensive analysis examines the fundamental characteristics and technical specifications that differentiate aluminum and copper transformers, exploring key aspects including conductivity, thermal properties, dimensional considerations, and practical applications across various sectors. Our detailed comparison will help professionals make informed decisions based on specific project requirements and operational constraints.
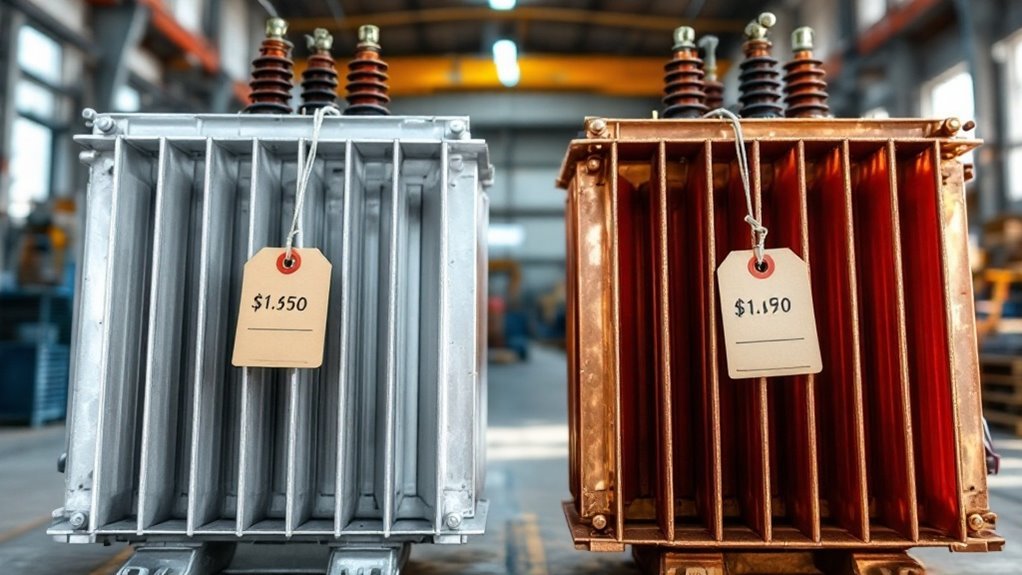
What Is Aluminium Transformer
An aluminium transformer uses aluminium windings instead of traditional copper in both its primary and secondary coils. The transformer’s core remains constructed from silicon steel laminations, while the conducting material for the windings is high-purity aluminium with specific electrical properties suitable for power transmission and distribution.
The aluminium windings undergo specialized manufacturing processes to maintain optimal electrical characteristics. Manufacturers typically increase the cross-sectional area of aluminium windings by approximately 60% compared to copper equivalents to compensate for aluminium’s lower conductivity. This design modification ensures adequate current-carrying capacity while maintaining transformer performance standards.
Modern aluminium transformers incorporate advanced insulation systems and cooling methods to manage operating temperatures effectively. The windings feature high-grade insulation materials, including kraft paper and mineral oil, which provide electrical isolation and heat dissipation. These transformers commonly use corrugated tanks and radiator systems for enhanced cooling efficiency.
What Is Copper Transformer
A copper transformer employs copper conductors for its primary and secondary windings. The transformer utilizes electrolytic grade copper with a minimum purity of 99.9%, ensuring superior electrical conductivity and reliable power transfer characteristics. The copper windings exhibit consistent performance across varying load conditions and operating temperatures.
The design of copper transformers benefits from copper’s inherent material properties. The windings maintain compact dimensions due to copper’s higher conductivity, allowing for efficient use of space within the transformer assembly. The copper conductors feature specialized enamel coatings and paper insulation systems that prevent electrical shorts while facilitating effective heat transfer.
These transformers implement precise winding techniques to minimize eddy current losses and optimize electromagnetic coupling between primary and secondary coils. The copper windings maintain their mechanical integrity over extended periods, resisting deformation under thermal stress and electromagnetic forces. Manufacturing processes include careful annealing and tension control to ensure uniform distribution of electrical and mechanical stresses throughout the winding assembly.
Key Differences Between Aluminium and Copper Transformers
Electrical Conductivity
The electrical conductivity of copper stands at 100% IACS (International Annealed Copper Standard), while aluminium reaches approximately 61% IACS. This difference means copper transformers exhibit lower electrical resistance, resulting in reduced power losses during operation. To compensate for aluminium’s lower conductivity, manufacturers must increase the cross-sectional area of aluminium windings by approximately 56% compared to copper windings to achieve equivalent current-carrying capacity.
Cost
Aluminium transformers typically cost 30-40% less than their copper counterparts due to lower raw material prices. The metal commodities market shows aluminium consistently maintaining a lower price per kilogram compared to copper. However, the total cost analysis should consider that aluminium transformers require larger windings and more insulation material to achieve comparable performance.
Weight
Aluminium’s density of 2.7 g/cm³ compared to copper’s 8.96 g/cm³ makes aluminium transformers approximately 50% lighter than equivalent copper units. This weight difference provides significant advantages in transportation, installation, and structural support requirements. A 1000 kVA aluminium transformer typically weighs 30-35% less than its copper equivalent.
Size
Due to aluminium’s lower conductivity, transformers using aluminium windings require larger cores and coils. The dimensional increase typically ranges from 15-25% compared to copper transformers of equivalent rating. This size difference affects installation space requirements and cooling considerations. For example, a 500 kVA aluminium transformer might need 20% more volume than its copper equivalent.
Thermal Conductivity
Copper’s thermal conductivity of 401 W/m·K surpasses aluminium’s 237 W/m·K, enabling more efficient heat dissipation in copper transformers. This superior heat management allows copper transformers to operate at higher current densities without overheating.
Durability and Strength
Copper exhibits superior mechanical strength with a tensile strength of 220-400 MPa compared to aluminium’s 70-180 MPa. This difference impacts the transformer’s resilience to mechanical stresses during transportation, installation, and operation. Copper transformers show better resistance to vibration and mechanical wear over time.
Efficiency
The higher conductivity of copper results in lower power losses and improved efficiency ratings. Copper transformers typically demonstrate 0.3-0.5% higher efficiency than comparable aluminium units. For a 1000 kVA transformer operating at full load, this efficiency difference can translate to several thousand kilowatt-hours saved annually.
Longevity
Copper transformers generally maintain operational integrity for 30-40 years, while aluminium transformers average 25-35 years under similar conditions. This lifespan difference stems from copper’s superior resistance to oxidation and mechanical stress. The connection points in aluminium transformers require more frequent maintenance due to thermal cycling effects.
Applications
Copper transformers predominate in applications demanding high reliability, such as medical facilities, data centers, and industrial processes. Aluminium transformers find widespread use in residential developments, commercial buildings, and utility distribution networks where cost optimization takes priority.