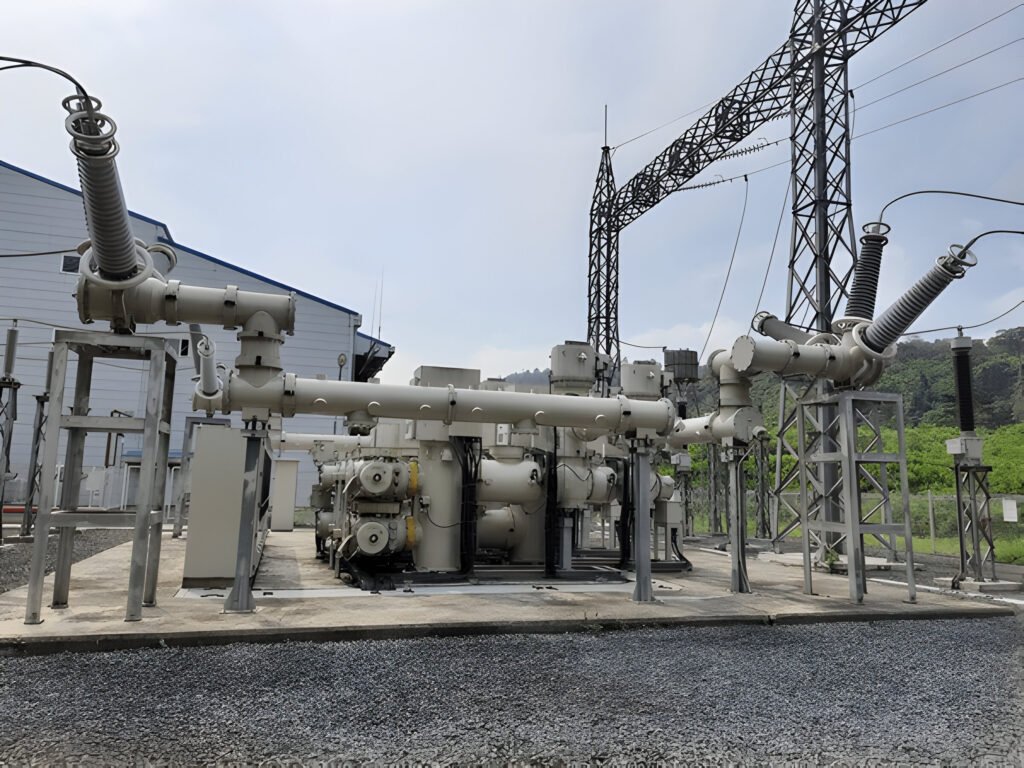
How Do You Test a Distribution Transformer
Testing a distribution transformer involves several key procedures. These include insulation testing, turns ratio and polarity tests, winding resistance measurement, no-load loss and excitation current tests, and load loss and impedance voltage tests. Each of these methods helps ensure the transformer’s functionality, safety, and efficiency before installation or after maintenance.
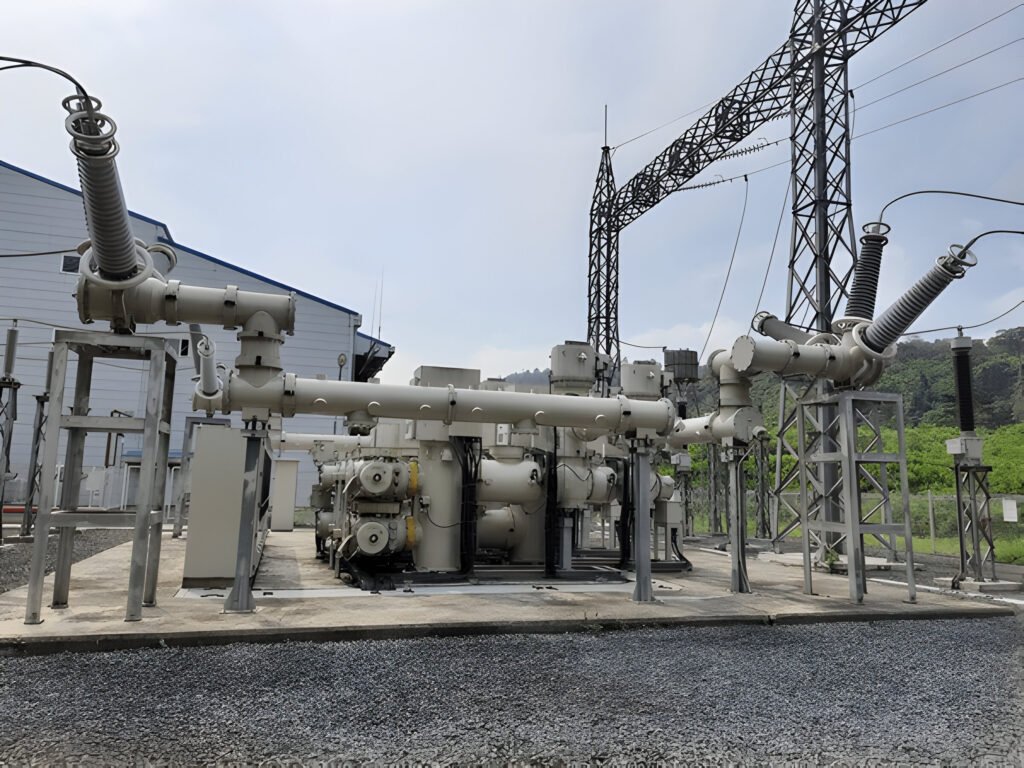
Insulation Testing
Insulation testing process involves assessing the integrity of the insulation system, which separates the conductive components within the transformer.
The primary method for insulation testing is the megger test, which utilizes a megohmmeter to measure insulation resistance. During this test, a high DC voltage is applied between the transformer’s windings and ground, as well as between different windings. The measured resistance values indicate the insulation’s condition.
Typical test voltages for distribution transformers range from 500V to 5000V, depending on the transformer’s voltage rating. The applied voltage should not exceed the manufacturer’s recommendations to prevent insulation damage.
Key parameters measured during insulation testing include:
- Insulation Resistance (IR): Expressed in megohms, this value should be above the minimum specified by industry standards.
- Polarization Index (PI): The ratio of insulation resistance measured at 10 minutes to that at 1 minute. A PI value greater than 2 generally indicates good insulation condition.
- Dielectric Absorption Ratio (DAR): Similar to PI, but using measurements at 60 seconds and 30 seconds. A DAR above 1.4 is considered acceptable.
Turns Ratio and Polarity Tests
Turns ratio and polarity tests are critical procedures in evaluating the performance and integrity of distribution transformers. These tests ensure that the transformer’s windings are correctly configured and functioning as designed.
The turns ratio test measures the relationship between the number of turns in the primary and secondary windings. This ratio directly correlates to the voltage transformation ratio of the transformer. To conduct this test, technicians apply a low voltage to the primary winding and measure the induced voltage in the secondary winding. The measured ratio should match the nameplate ratio within acceptable tolerances, typically ±0.5%.
Polarity testing determines the relative instantaneous direction of the induced voltages in the transformer windings. Technicians perform polarity tests using either the AC or DC method. In the AC method, voltages are measured between specific terminals to confirm the polarity. The DC method involves applying a DC voltage to the primary winding and observing the deflection of a voltmeter connected to the secondary winding.
Winding Resistance Measurement
Winding resistance measurement is a critical test in evaluating the condition of a distribution transformer. This test helps identify potential issues such as loose connections, broken strands, or high-resistance joints within the transformer windings.
The measurement process involves applying a DC current to each winding and measuring the resulting voltage drop. Using Ohm’s Law (V = IR), technicians can calculate the resistance of each winding.
Typically, the resistance is measured for all windings, including the primary (high voltage) and secondary (low voltage) windings. For three-phase transformers, measurements are taken between each pair of terminals (e.g., H1-H2, H2-H3, H3-H1 for the high voltage side).
The measured resistance values are then compared to the manufacturer’s specifications or previous test results. Deviations exceeding 5% from the expected values may indicate a problem that requires further investigation.
As copper has a positive temperature coefficient, its resistance increases with temperature. To ensure accurate comparisons, resistance measurements are typically corrected to a standard temperature, usually 75°C for distribution transformers.
The correction formula is:
R75 = Rt [((235 + 75) / (235 + t)]
Where:
- R75 = Resistance at 75°C
- Rt = Measured resistance at temperature t
- t = Winding temperature at the time of measurement
No-Load Loss and Excitation Current
No-load loss, also known as core loss, occurs in the transformer’s magnetic core when it is energized but not supplying power to a load. This loss consists of two main components:
- Hysteresis loss: Caused by the continuous magnetization and demagnetization of the core material.
- Eddy current loss: Resulting from circulating currents induced in the core by the alternating magnetic field.
To measure no-load loss, the transformer’s primary winding is energized at rated voltage while the secondary winding remains open-circuited. The power input to the primary winding under these conditions represents the no-load loss.
Excitation current, also called magnetizing current, is the current drawn by the transformer’s primary winding when energized at rated voltage with no load connected. This current is responsible for establishing the magnetic field in the core and is typically 1-5% of the transformer’s rated current.
Load Loss and Impedance Voltage
Load loss testing measures the power dissipated in the transformer’s windings and other components when carrying full-rated current. This test is typically conducted by short-circuiting the secondary winding and applying a voltage to the primary winding sufficient to circulate rated current through both windings. The power input required to maintain this current flow represents the load loss.
Impedance voltage, also known as short-circuit voltage, is determined during the load loss test. It is the voltage required to circulate rated current through the transformer windings with the secondary short-circuited. Impedance voltage is usually expressed as a percentage of the rated voltage and is a key parameter in determining the transformer’s behavior under various load conditions.