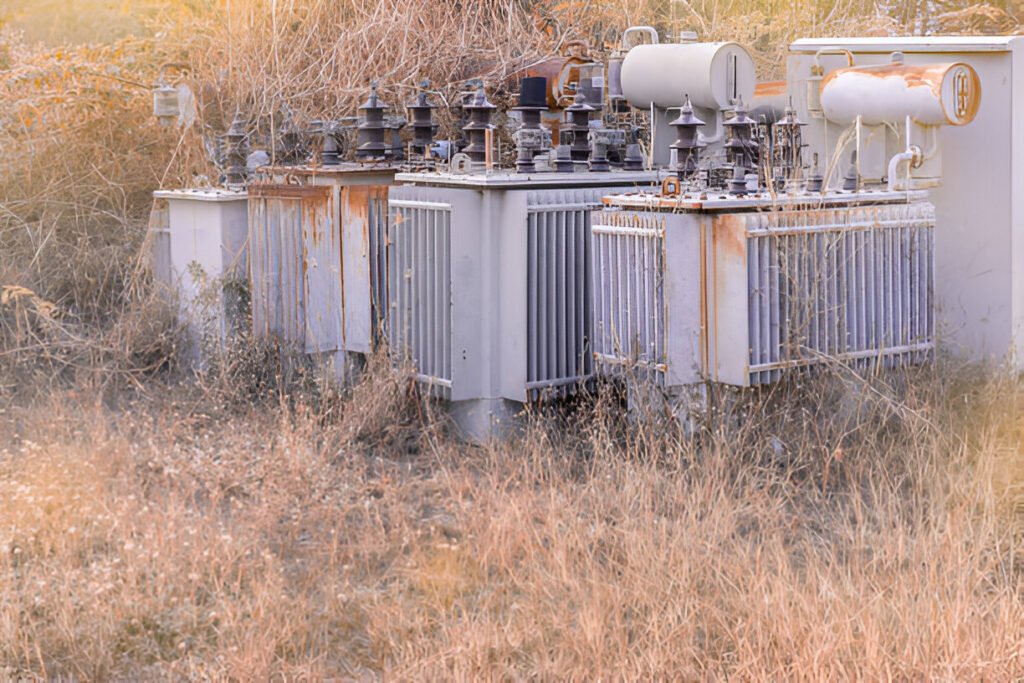
Guide to Electrical Transformer
Electrical transformers are essential components in power transmission and distribution systems, enabling the efficient transfer of electrical energy across vast distances. These devices play a crucial role in stepping up or down voltage levels, ensuring that electricity is delivered safely and effectively to homes, businesses, and industrial facilities.
In this comprehensive guide, we will delve into the fundamental principles, design considerations, and practical applications of electrical transformers. From understanding the basic structure and types of transformers to exploring their role in modern power grids, this article aims to provide a thorough overview of these indispensable machines.
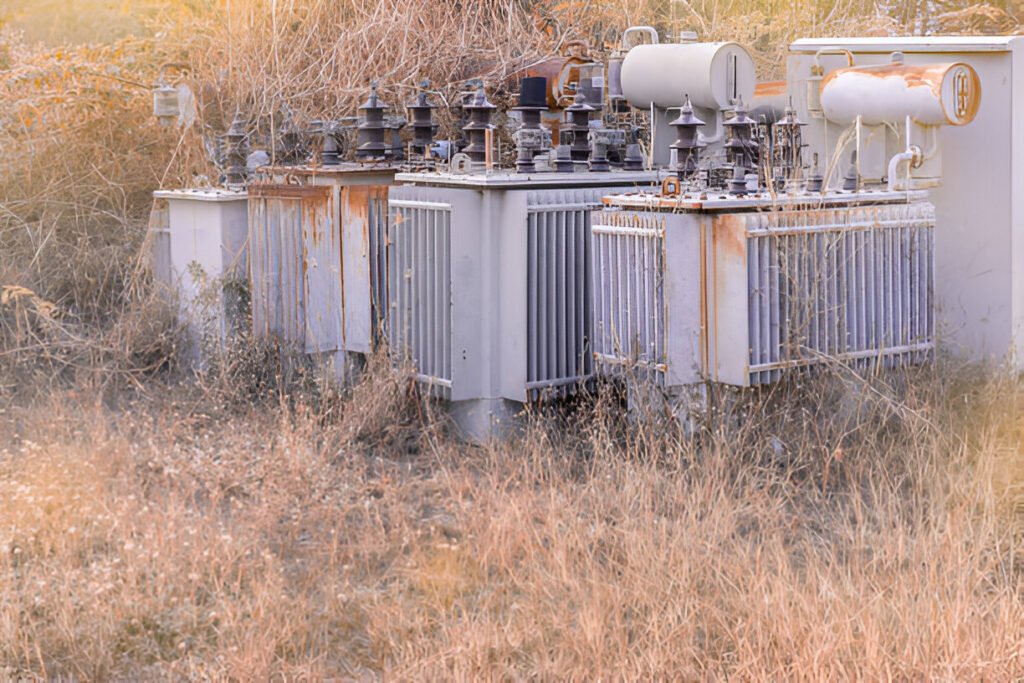
What Is an Electric Transformer
An electrical transformer is a critical component in power systems that enables the efficient transmission and distribution of electrical energy. This static electrical device converts alternating current (AC) from one voltage level to another through electromagnetic induction.
At its core, a transformer consists of two or more coils of insulated copper wire wound around an iron core. The primary winding receives electrical power from the source, while the secondary winding delivers the transformed voltage to the load. The iron core provides a path for the magnetic flux, coupling the windings and facilitating the voltage transformation process.
Functions of Electrical Transformers
- Voltage Transformation: Transformers step up or step down voltage levels to optimize power transmission and distribution efficiency. Step-up transformers increase voltage for long-distance transmission, minimizing current and reducing power losses. Step-down transformers decrease voltage to safe levels for end-user equipment and household appliances.
- Isolation: Transformers provide electrical isolation between circuits, preventing direct current (DC) flow and ensuring safety. Isolation transformers protect sensitive electronic components from voltage spikes, transients, and electrical noise.
- Current Transformation: In addition to voltage transformation, transformers can also change current levels. Current transformers (CTs) are used to measure and monitor current in electrical systems, providing essential data for protection systems and energy meters.
- Power Distribution: Distribution transformers are crucial in power distribution systems, converting high-voltage electricity from transmission lines to lower voltages suitable for local distribution and end-user consumption.
- Impedance Matching: Transformers can match the impedance of source and load circuits, maximizing power transfer efficiency and minimizing reflections in audio systems, telecommunications, and high-frequency applications.
Working Principle of Electrical Transformers
The working principle of electrical transformers is based on Faraday’s Law of Electromagnetic Induction. When an alternating current flows through the primary winding, it creates a varying magnetic field in the transformer core. This magnetic field induces an electromotive force (EMF) in the secondary winding, generating an output voltage proportional to the turn ratio between the windings.
The voltage transformation occurs without any direct electrical connection between the primary and secondary windings. The ratio of the number of turns in the primary coil to the number of turns in the secondary coil determines the voltage transformation ratio. For a step-up transformer, the secondary winding has more turns than the primary, resulting in a higher output voltage. Conversely, a step-down transformer has fewer turns in the secondary winding, producing a lower output voltage.

Components of Electric Transformers
Core
The core is a fundamental component of an electrical transformer, typically made from laminated sheets of high-permeability ferromagnetic material, such as silicon steel.
The purpose of the core is to provide a low-reluctance path for the magnetic flux generated by the transformer’s windings. This helps to minimize energy losses and improve the overall efficiency of the transformer.
Windings
The windings are consisting of insulated copper wire coils wrapped around the core. There are two types of windings in a transformer: the primary winding, which receives the input voltage, and the secondary winding, which delivers the output voltage to the load. The ratio of turns between the primary and secondary windings determines the voltage transformation ratio, allowing transformers to step up or step down the voltage as needed.
Insulation Agents
Insulation agents, such as transformer oil, epoxy resin, or air, provide electrical insulation between the windings and the core, as well as between the windings themselves. Proper insulation helps to prevent short circuits, reduce electrical noise, and protect the transformer from the damaging effects of moisture, dust, and other environmental factors. In oil-immersed transformers, the insulating oil also serves as a cooling medium, helping to dissipate heat generated by the windings and core during operation.
Tap Changer
Tap changers are mechanical devices used in some transformers to regulate the output voltage under varying load conditions. They allow for small adjustments to be made to the number of turns in the transformer’s windings, effectively changing the voltage ratio. This is particularly useful in applications where a constant voltage level needs to be maintained despite fluctuations in the load or input voltage.
Tap changers can be either manual or automatic, with the latter being more common in larger power transformers used in distribution systems.
Cooling System
As transformers operate, they generate heat due to copper losses in the windings and iron losses in the core. To prevent overheating and potential damage, transformers employ various cooling systems, such as:
- Oil-immersed transformers: These transformers use insulating oil as a cooling medium, which circulates through the windings and core, absorbing and dissipating heat.
- Dry-type transformers: These transformers rely on air circulation for cooling, often aided by fans or heat sinks to improve heat dissipation.
- Water-cooled transformers: In some large power transformers, a separate water-cooling system is used to remove heat from the insulating oil, providing an additional level of cooling capacity.
Transformer Tank
The transformer tank is a protective enclosure that houses the core, windings, insulation, and cooling system. Its primary functions are to contain the insulating oil (in oil-immersed transformers), protect the internal components from the external environment, and provide a means for mounting the transformer securely.
Types of Electrical Transformers
Core-Type Transformer and Shell-Type Transformer
In a core-type transformer, the primary and secondary windings are wound around a central laminated iron core. The coils are placed on separate limbs of the core, with the primary winding on one side and the secondary winding on the other. This design allows for efficient magnetic flux linkage between the windings and the core, resulting in lower losses and improved performance.
Shell-type transformers feature windings that are surrounded by the magnetic core. The primary and secondary coils are placed side by side, with the laminated iron core forming a shell around them. This configuration provides better mechanical protection for the windings and offers improved magnetic shielding, making shell-type transformers suitable for applications requiring low electrical noise and reduced interference.
Step-Up Transformer and Step-Down Transformer
A step-up transformer is designed to increase the voltage level from the primary winding to the secondary winding while decreasing the current. This is achieved through electromagnetic induction, where the primary coil has fewer turns than the secondary coil. Step-up transformers play a vital role in power transmission, as higher voltages allow for reduced power losses and more efficient energy transfer over long distances.
A step-down transformer reduces the voltage level from the primary winding to the secondary winding while increasing the current. In this case, the primary coil has more turns than the secondary coil. Step-down transformers are commonly used in power distribution systems to bring the high transmission voltages down to levels suitable for household consumption and industrial applications.
Single-Phase Transformer and Three-Phase Transformer
Single-phase transformers are designed to operate with a single-phase power supply, making them suitable for smaller-scale applications such as residential power distribution, lighting systems, and small electronic devices. They consist of a single primary winding and a single secondary winding, along with a magnetic core to facilitate electromagnetic induction.
Three-phase transformers are used in more demanding industrial applications and power distribution systems. They are designed to handle three-phase electrical power, which is more efficient and economical for transmitting large amounts of energy. Three-phase transformers consist of three sets of primary and secondary windings, each connected to one phase of the power supply. This configuration allows for balanced power distribution and reduced copper losses compared to using three single-phase transformers.
Power Transformer, Distribution Transformer, and Instrumentation Transformer
Power transformers are large, high-capacity transformers used in power transmission systems. They are typically found in substations and are responsible for stepping up the voltage for long-distance transmission and then stepping it down for distribution to end-users. Power transformers are designed to handle high voltage levels and substantial power ratings, often ranging from several hundred kVA to hundreds of MVA.
Distribution transformers are smaller units that are used to further step down the voltage from the transmission levels to levels suitable for end-user equipment. These transformers are commonly mounted on utility poles or placed in pad-mounted enclosures near the point of consumption.
Instrumentation transformers, also known as measurement transformers or instrument transformers, are specialized transformers used for measuring and monitoring electrical quantities such as voltage, current, and power. They provide isolated and scaled-down replicas of the primary electrical quantities, allowing for safe and accurate measurement by protective relays, energy meters, and other monitoring devices.

Applications of Electrical Transformers
- Power Distribution: Step-up transformers are used in power generation plants to increase the voltage level for long-distance transmission, minimizing power losses. Step-down transformers then reduce the voltage to suitable levels for household consumption and industrial use. Distribution transformers, often seen on utility poles, further step down the voltage for local distribution.
- Isolation and Safety: Isolation transformers provide electrical isolation between circuits, ensuring safety and preventing ground loops. They are commonly used in medical equipment, laboratory instruments, and audio systems to protect against electrical shock and minimize noise interference.
- Voltage Regulation: Transformers with tap changers allow for adjustable output voltage, ensuring a constant voltage level despite load fluctuations.
- Instrument Transformers: Specialized transformers, such as current transformers and potential transformers, are used in metering and protection applications. They provide accurate measurements of current and voltage for energy metering, fault detection, and system monitoring.
- Power Conversion: Transformers are used in various power conversion applications, such as in rectifiers, inverters, and switch-mode power supplies. They enable efficient conversion between AC and DC voltages and help regulate output voltages.
- Audio and Signal Processing: Audio transformers are used in audio systems to provide impedance matching, signal isolation, and balanced-to-unbalanced signal conversion. They ensure optimal signal quality and prevent ground loops and electromagnetic interference.
Safety Tips to Consider When Working with Transformers
- Personal Protective Equipment (PPE): Always wear appropriate PPE when working with transformers.
- De-energize and Lockout/Tagout: Before conducting any maintenance, repairs, or inspections, completely de-energize the transformer and associated electrical systems.
- Maintain Safe Clearance: Transformers generate strong electromagnetic fields, which can induce high voltages and currents in nearby conductive objects.
- Grounding and Bonding: Ensure that the transformer core, tank, and secondary windings are securely grounded.
How Do I Know What Transformer to Use
When determining the appropriate transformer, consider the following key points:
- Input Voltage and Output Voltage: Identify the voltage of the power source (primary voltage) and the desired voltage for the load equipment (secondary voltage). This will help you choose between a step-up transformer, which increases voltage, or a step-down transformer, which decreases voltage.
- Single-Phase or Three-Phase: Assess whether your application requires a single-phase transformer, commonly used for household consumption levels and lighter loads, or a three-phase transformer, suitable for industrial applications and heavier loads.
- Insulation Type: Consider the environment and application requirements when choosing between dry-type transformers, which use air or epoxy resin insulation, or liquid-filled transformers, which use oil or other dielectric fluids for cooling and insulation.
- Mounting and Installation: Determine the physical space available and the mounting requirements for the transformer. Options include pole-mounted transformers, pad-mounted transformers, and substation transformers.
FAQs
Where Is the Electric Transformer Located
Electric transformers are typically located on utility poles, in underground vaults, or in substations. Pole-mounted transformers are common in residential areas, while pad-mounted or underground transformers are used in commercial and industrial settings.
How Long Does It Take to Replace an Electric Transformer
Replacing an electric transformer can take anywhere from a few hours to several days, depending on the size, location, and complexity of the installation.
What Is the Price of an Electric Transformer
Small, single-phase transformers for residential use can cost a few hundred dollars, while large, three-phase transformers for industrial applications can cost tens of thousands of dollars or more.
What Is the Cost to Repair an Electrical Transformer
The cost to repair an electrical transformer depends on the extent of the damage and the required parts and labor. Minor repairs, such as replacing a fuse or a damaged wire, can cost a few hundred dollars. More extensive repairs, like rewinding coils or replacing the core, can cost several thousand dollars.
How Can a Bad Transformer Affect My Electric Bill
A bad transformer can cause inefficient power transmission, leading to higher energy losses and increased electricity consumption. This inefficiency can result in higher electric bills. Additionally, a malfunctioning transformer may cause power fluctuations or outages, which can damage appliances and electronic devices, indirectly affecting electric bills.
Why Does My Electrical Transformer Explode
Electrical transformers can explode due to various reasons, including lightning strikes, overloading, insulation failure, or mechanical damage. When a transformer fails, the sudden release of energy can cause an explosion, often accompanied by a loud noise and a bright flash.
Do Electrical Transformers Need Oil
Many electrical transformers, particularly large power transformers, use oil as an insulating and cooling medium. The oil helps to dissipate heat generated during the transformer’s operation and prevents electrical discharges between the windings. However, some transformers, such as dry-type transformers, use other insulating materials like epoxy resin or air instead of oil.