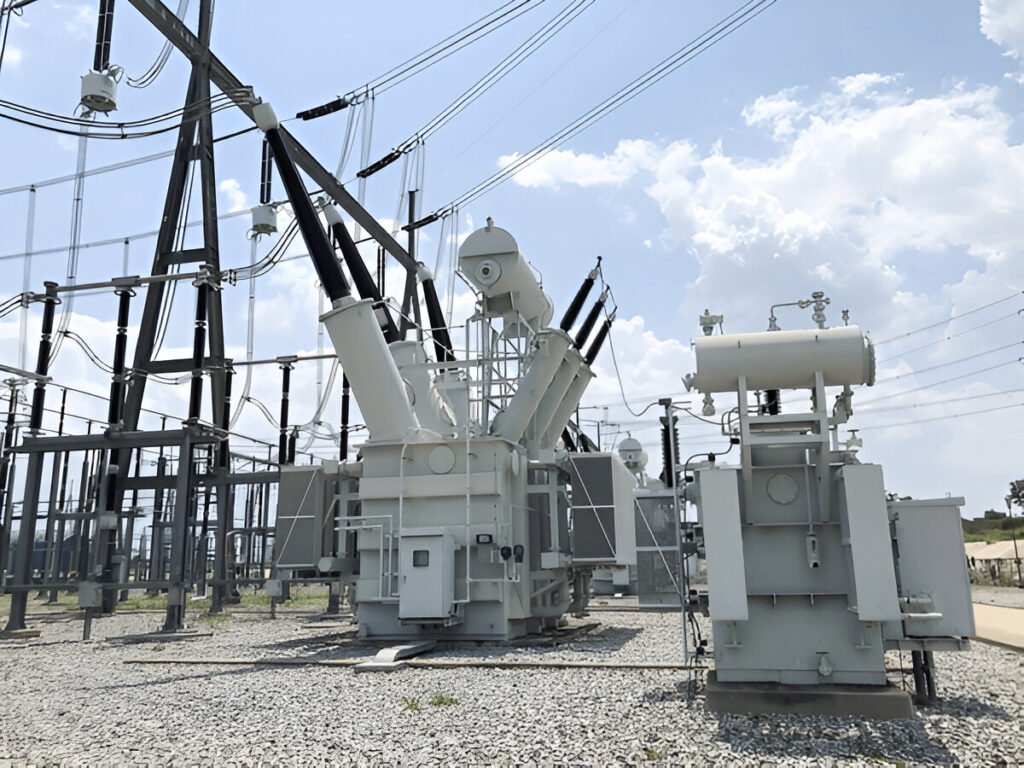
Can You Run a Transformer Without a Load
Running a transformer without a load, also known as no-load operation, is a common occurrence in electrical power systems. Although transformers are designed to transfer power efficiently between circuits, there are instances when they may operate without any connected load.
This article explores the concept of no-load operation, its characteristics, and the implications for transformers running under such conditions.
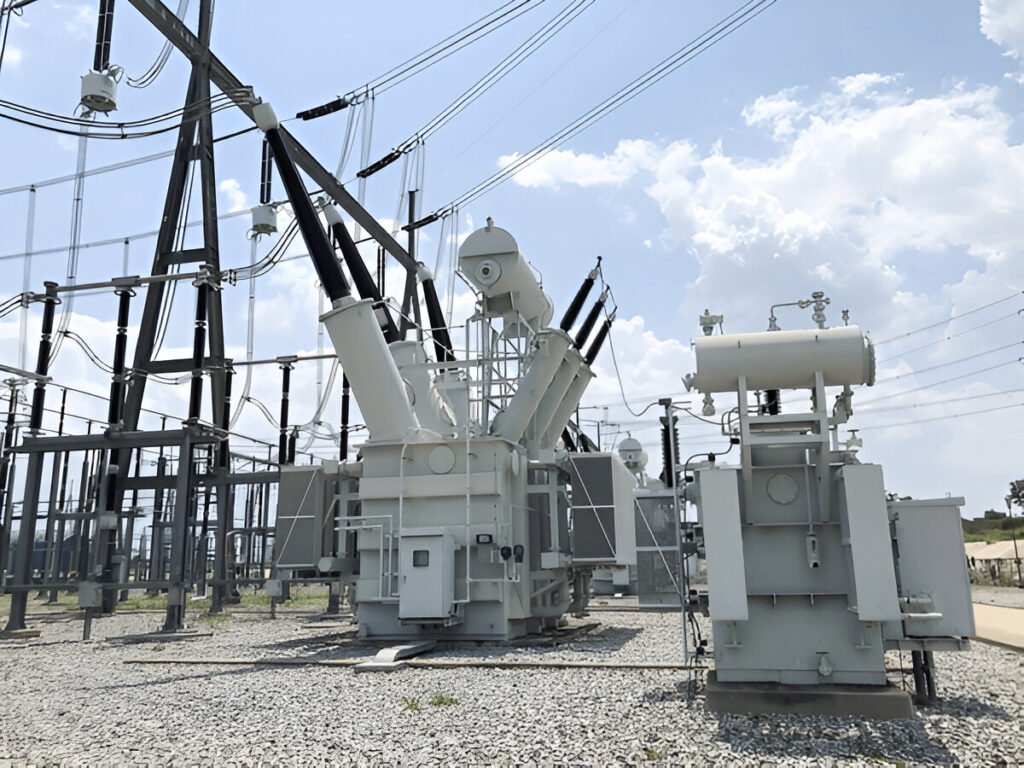
What Is No-Load Condition
No-load condition refers to the state of a transformer when it is energized but not connected to any load on the secondary winding. In this state, the transformer’s primary winding is connected to the power source, while the secondary winding remains open-circuited. The absence of a load means that no current flows through the secondary winding, and consequently, no power is transferred to an external circuit.
No-Load Current
Despite the absence of a load, a small current still flows through the primary winding during no-load operation. This current is referred to as the no-load current or the magnetizing current. The no-load current is essential for maintaining the transformer’s magnetic flux and accounts for the core losses that occur even in the absence of a load.
Consists of No-Load Current
Magnetizing Component
The magnetizing component of the no-load current is responsible for establishing and maintaining the magnetic flux within the transformer’s core. It is a reactive current that lags the applied voltage by 90 degrees.
Active Component
In addition to the magnetizing component, the no-load current also includes an active component. This active component represents the power losses that occur in the transformer’s core due to hysteresis and eddy currents. These losses are present even in the absence of a load and contribute to the overall no-load losses of the transformer.
Characteristics of No-Load Operation
No-Load Current
The no-load current in a transformer is typically much smaller than the rated current under normal loading conditions. It is usually expressed as a percentage of the rated primary current and can range from less than 1% for large power transformers to around 10% for smaller distribution transformers.
Core Losses in No-Load Condition
During no-load operation, core losses constitute the primary source of power loss in a transformer. Core losses consist of hysteresis losses and eddy current losses. Hysteresis losses occur due to the cyclic magnetization and demagnetization of the core material, while eddy current losses arise from induced currents circulating within the core. These losses manifest as heat dissipation in the core and contribute to the transformer’s no-load power consumption.
Implications of Running a Transformer Without Load
Reduced Efficiency
Running a transformer without a load results in reduced overall efficiency. Since the transformer continues to consume power to maintain the magnetic flux and compensate for core losses, the absence of useful power transfer to a load leads to a lower efficiency compared to normal operating conditions. The no-load losses represent a constant power draw that affects the transformer’s efficiency, especially at low loading levels.
Voltage Regulation
In no-load condition, the transformer’s secondary voltage is typically higher than its rated value. This is because the absence of a load means there is no voltage drop across the transformer’s windings due to load current. The no-load voltage is determined by the transformer’s turns ratio and the applied primary voltage. When a load is connected, the secondary voltage drops as the load current increases, resulting in voltage regulation.
Inrush Current
When a transformer is energized without a load, it experiences an inrush current in the primary winding. The inrush current is a transient phenomenon that occurs due to the saturation of the transformer’s core during the initial energization. The magnitude of the inrush current can be several times higher than the rated current and can cause stress on the transformer’s windings and protective devices.
Overheating
Although running a transformer without a load may seem less stressful compared to full-load operation, it can still lead to overheating issues. The no-load losses, primarily the core losses, generate heat within the transformer. In the absence of a load, there is no power transfer to dissipate this heat, leading to a gradual temperature rise. Prolonged operation without a load can cause the transformer to overheat, potentially damaging the insulation and reducing the transformer’s lifespan.
Reduced Power Factor
In no-load condition, the transformer’s power factor is significantly lower compared to loaded operation. The no-load current is predominantly reactive, with a high magnetizing component and a small active component. This results in a poor power factor, typically less than 0.1. The low power factor during no-load operation can have implications for the overall power system, such as increased reactive power consumption and reduced system efficiency.